
Historical Context and Origins
The concept of assembly lines dates back to ancient times when early civilization developed ways to streamline production. Ancient techniques in Egypt and China saw workers responsible for specific tasks in producing complex items like textiles and weapons. Fast forward to the 18th and 19th centuries, innovations such as Eli Whitney's cotton gin laid the foundation for modern assembly line concepts.
The Industrial Revolution
During the Industrial Revolution, key developments changed how goods were produced. One of the most significant advances was the introduction of mechanized production. Factories began employing steam-powered machines, drastically increasing output and efficiency. This era also saw the inception of principles that would lead to contemporary assembly lines.
Core Principles of Assembly Lines
A fundamental principle is the division of labor, where specialized tasks allow workers and machinery to perform specific functions repeatedly. Specialization leads to improved efficiency, reducing time lost transitioning between diverse tasks. Another core principle is sequential production, a step-by-step method ensuring a continuous flow of materials and products through the production process.
Division of Labor
The specialization inherent in assembly lines enhances productivity. Workers focus on limited tasks, becoming experts in their roles, which minimizes errors and speeds up operations.
Sequential Production
This principle involves arranging processes in a logical sequence so each step follows smoothly from the last. Materials and products move through stages efficiently, helping ensure consistency and uniformity in the final product.
Design and Operation
Assembly lines consist of various components crucial for their function. Machinery and equipment form the backbone, with workstations and tools optimized to support specific tasks. Workflow optimization includes strategic layout design to minimize unnecessary movement and quickly identify potential bottlenecks, effectively managing them to maintain a steady production pace.
Components of an Assembly Line
Critical components include meticulously arranged workstations equipped with necessary tools, while advanced machinery handles repetitive or strenuous tasks. The synergy of these elements results in an efficient production system.
Workflow Optimization
Optimizing workflow, including layout design, ensures minimal wasted effort and reduces delays. Identifying and managing bottlenecks quickly helps maintain smooth production, enhancing overall efficiency.
Technological Advances
Modern assembly lines have benefited significantly from technological advancements, particularly automation and robotics. Integration of Artificial Intelligence (AI) and Machine Learning has further refined operations, although human workers remain vital for oversight, problem-solving, and nuanced tasks requiring judgment. Real-time monitoring and data analytics provide insights, while sensors and IoT enable predictive maintenance, preventing downtime and extending machine life.
Automation and Robotics
The use of robots and automated systems has revolutionized assembly lines, taking over monotonous or dangerous tasks and freeing humans for more complex duties.
Real-time Monitoring and Data Analytics
Sensors and interconnected devices offer real-time performance data, improving decision-making and allowing proactive maintenance, thus enhancing reliability and efficiency.
Benefits and Challenges
Assembly lines present several advantages, such as increased productivity, cost reduction, and stringent quality control. However, they are not without challenges. Potential drawbacks include monotony for workers leading to fatigue, initial setup costs, and issues concerning flexibility in production changes.
Advantages
The primary benefits include heightened productivity due to rapid, continuous production, reduced costs through efficiency, and strict quality standards ensuring consistent output.
Potential Drawbacks
Challenges can arise in the form of worker dissatisfaction due to repetitive tasks, substantial investment required for setup, and difficulties adapting to varied production demands.
Applications Across Industries
Assembly lines are applicable across various industries. In automotive manufacturing, they've historically transformed vehicle production and continue to evolve with modern practices. In electronics and consumer goods, precision and speed are paramount. In food and beverage production, maintaining hygiene and safety standards is crucial to meet industry regulations.
Automotive Manufacturing
From Henry Ford's revolutionary approach to today's energy-efficient electric vehicle assembly plants, the automotive industry showcases the evolution of assembly line applications.
Electronics and Consumer Goods
In this sector, assembly lines must balance speed with precise calibration to produce reliable, high-quality products rapidly.
Food and Beverage Production
Hygiene and safety are critical; thus, assembly lines here incorporate stringent sanitary measures alongside efficiency-driving technologies.
Future Trends
Industry 4.0 marks the emergence of smart factories where interconnected systems enhance customization and flexibility. Environmental considerations drive the adoption of sustainable practices aimed at boosting energy efficiency and reducing waste.
Industry 4.0 and Smart Factories
These facilities utilize interconnected systems, AI, and flexible production methods to adapt quickly to market demands while maintaining optimal efficiency.
Environmental Considerations
Sustainability is increasingly important. Modern lines aim to reduce energy usage and material wastage, contributing to environmental conservation efforts.
Practical Insights
Case studies highlight success stories from leading companies demonstrating innovative implementations of assembly lines. Key lessons learned emphasize the importance of workforce training and development, alongside best practices in continuous improvement techniques, ensuring adaptation and growth despite evolving challenges.
Case Studies
Examining various case studies reveals valuable lessons. Successful companies invest in employee training and foster environments encouraging innovation and efficiency.
Best Practices for Implementation
Effective implementation necessitates thorough training programs, ongoing skill enhancement, and embracing continuous improvement strategies to navigate and excel amidst changing dynamics.
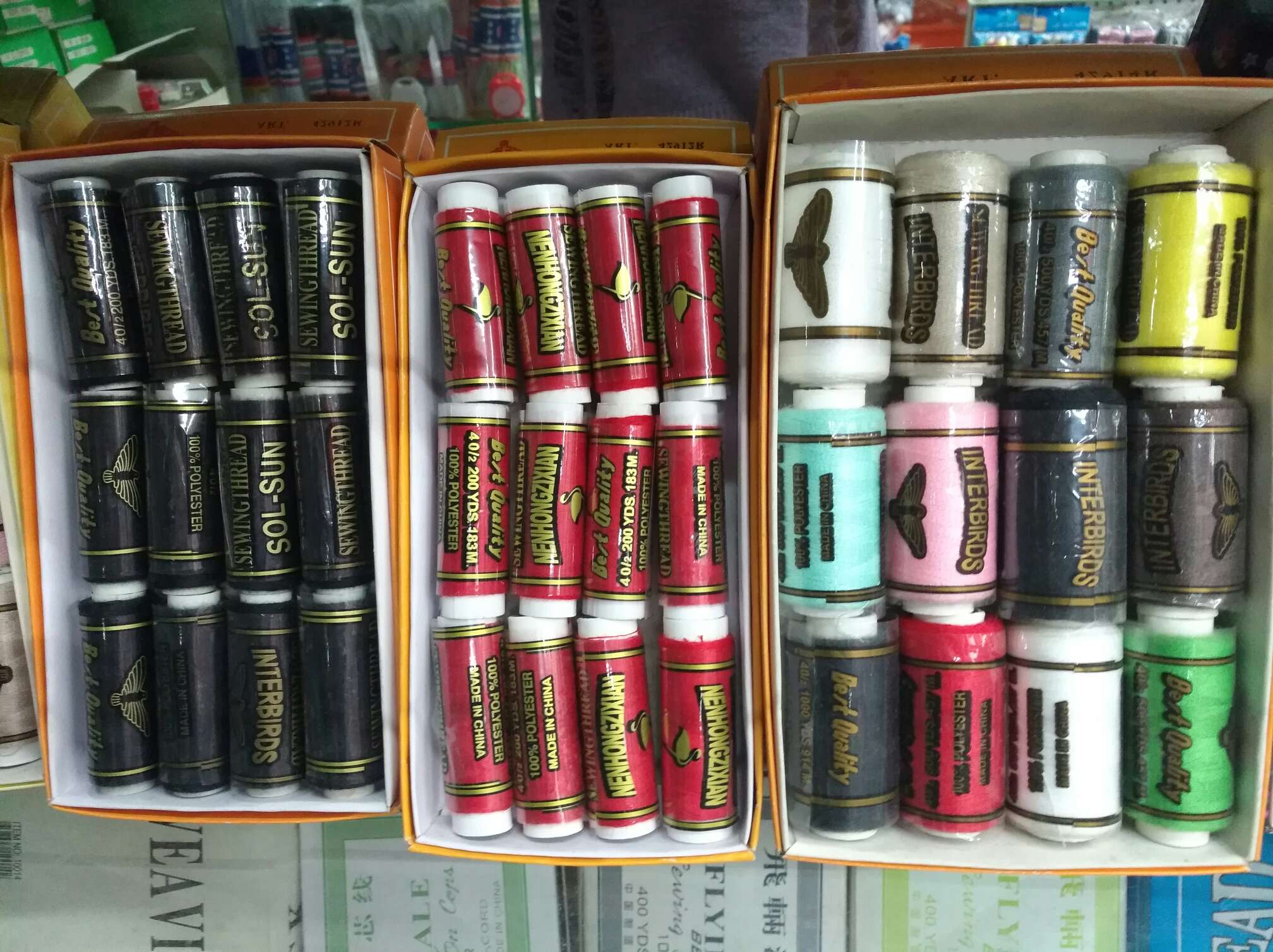