
Definition and Importance of Advanced Assembly Lines
Advanced assembly lines represent a significant evolution in manufacturing processes, leveraging cutting-edge technologies to optimize production. By integrating automation, robotics, digital twins, and IoT (Internet of Things), these sophisticated systems enhance efficiency, reduce errors, and increase output quality. Implementing advanced assembly lines provides numerous benefits including reduced labor costs, increased precision, faster production times, and improved adaptability to market changes.
Key technologies involved include programmable logic controllers (PLCs), real-time data analytics, machine learning algorithms, and advanced sensors. Together, these components form an interconnected ecosystem that drives productivity and innovation in modern manufacturing landscapes.
Tesla's Gigafactory
The Gigafactory, launched by Tesla, stands as a beacon of innovation within the automotive industry. Built to produce electric vehicle batteries at scale, this facility employs extensive automation and robotics. Automated guided vehicles (AGVs) efficiently transport materials across the plant, while robotic arms handle intricate tasks with unmatched precision.
This high level of automation has resulted in remarkable improvements in production efficiency and output. The factory can produce thousands of battery packs daily, directly contributing to Tesla's ability to meet growing demand. However, this journey was not without challenges. Initial setup issues such as synchronization between robots and human workers were resolved by fine-tuning software algorithms and implementing collaborative robot systems (cobots).
Toyota's Lean Manufacturing
Toyota pioneered lean manufacturing principles, focusing on minimizing waste while maximizing value. This approach encompasses various strategies, including Just-In-Time (JIT) production, continuous improvement (Kaizen), and smart inventory management. Each technique aims to create a seamless flow of products from inception to delivery.
The adoption of lean methodologies has yielded substantial improvements in both speed and quality of production. By eliminating non-essential processes, Toyota streamlined its operations, thus reducing lead times and enhancing product consistency. Furthermore, the sustainability of lean practices ensures long-term benefits, including reduced environmental impact and ongoing cost savings.
Siemens' Digital Factory
Siemens has fully embraced digital transformation within their manufacturing framework, notably through their "Digital Factory" concept. This initiative leverages digital twins—virtual replicas of physical entities—and IoT technologies to orchestrate complex assembly line processes.
The use of digital twins facilitates real-time monitoring and simulation, enabling swift adjustments and customization based on consumer needs. Consequently, Siemens achieves heightened flexibility and tailored production capabilities, meeting diverse market demands with agility. Measurable outcomes showcase increased responsiveness, enhanced product variety, and optimized resource usage.
Key Takeaways from the Case Studies
Examining these case studies reveals common success factors in the deployment of advanced assembly lines. Crucial elements include comprehensive planning, investment in state-of-the-art technology, and fostering a culture of continuous improvement. Each company’s experiences underscore the importance of addressing initial challenges promptly and leveraging data-driven insights for informed decision-making.
For instance, Tesla's emphasis on overcoming synchronization issues showcases the need for resilience and adaptability. Toyota highlights how traditional principles like lean manufacturing can coexist with modern advancements to yield superior results. Siemens exemplifies the potential for digital solutions to revolutionize production dynamics comprehensively.
Manufacturers aspiring to emulate these successes should consider prioritizing strategic technological integrations, ensuring employee upskilling, and maintaining a commitment to iterative enhancements.
The Future of Advanced Assembly Lines
As industries evolve, so too will the landscape of advanced assembly lines. Emerging trends point towards greater incorporation of artificial intelligence (AI), predictive maintenance powered by big data analytics, and further advancements in 3D printing. These developments promise to elevate efficiency, customize mass production, and minimize downtime proactively.
The ripple effects of these innovations extend beyond manufacturing, influencing sectors such as healthcare, aerospace, and electronics. Enhanced versatility, paired with sustainable practices, positions advanced assembly lines as pivotal drivers of future industrial transformations. Anticipations for the next decade envision increasingly autonomous factories, harmonized global supply chains, and revolutionary product design frameworks.
Resources and Further Reading
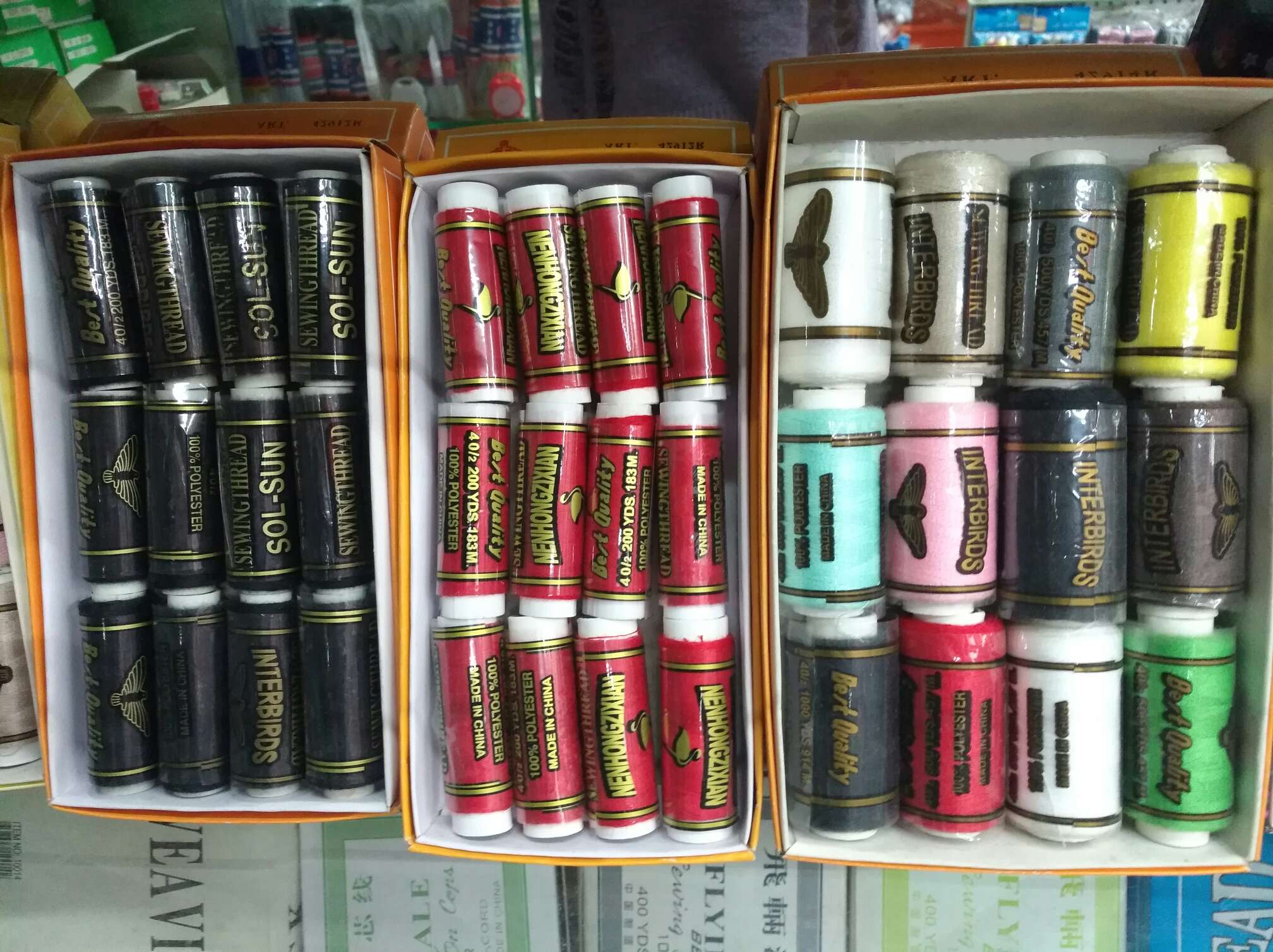