
In the world of manufacturing, industry standards are a cornerstone that ensures product integrity, safety, and reliability. These standards define specific criteria for production processes and outcomes, providing a uniform foundation upon which quality expectations are built. Meeting these stringent guidelines is essential not only for maintaining consumer trust but also for regulatory compliance and preserving market competitiveness.
High-precision assembly lines play an instrumental role in this quest for excellence. Unlike traditional assembly lines that may rely more heavily on manual labor and less accurate machinery, high-precision assembly lines leverage advanced technologies to achieve meticulous accuracy and consistency in production. This leap in precision has been made possible through innovations such as automated machinery, sophisticated sensors, and integrated control systems, setting a new bar for what is achievable in modern manufacturing.
The backbone of high-precision assembly lines lies in their technological sophistication. Automated machinery and robotics bring unprecedented speed and repeatability to the assembly process, minimizing human error and variability. Precision sensors and measurement systems continually monitor and adjust the operations, ensuring every component meets exact specifications. Furthermore, software and control system integrations provide seamless orchestration of these elements, allowing real-time data analysis and adaptive control, thus fine-tuning each step of the production cycle.
The benefits of adopting high-precision assembly lines are manifold. Enhanced product quality and consistency emerge as primary advantages, as tighter tolerances translate into superior end products. Manufacturing defects and waste are significantly reduced, leading to cost savings and a more sustainable production model. Additionally, these cutting-edge lines increase overall production efficiency and speed, allowing manufacturers to meet growing demands without compromising on quality.
Numerous case studies from diverse sectors illustrate the transformative impact of high-precision assembly lines. In the automotive industry, for instance, the deployment of such lines has led to remarkable improvements in vehicle performance and reliability. Electronics manufacturers have seen significant decreases in defect rates, resulting in higher consumer satisfaction and lower return rates. The aerospace sector, where precision is non-negotiable, continues to benefit immensely from these advancements, achieving quantum leaps in both safety and productivity. Success stories abound, highlighting quantitative enhancements in various metrics including cycle times, yield rates, and operational costs.
However, implementing high-precision assembly lines isn't without its challenges. Common obstacles include substantial upfront investment in technology and infrastructure, complexities around integration, and disruptions during the transition phase. Overcoming these hurdles requires strategic planning and resource allocation. Engaging cross-functional teams early in the design phase, conducting thorough feasibility studies, and securing buy-in from all stakeholders can mitigate many risks. Moreover, workforce training and skill development are crucial; empowering employees with the knowledge to operate and maintain these sophisticated systems ensures smoother adoption and sustained success.
Looking ahead, several emerging technologies promise to further revolutionize high-precision assembly lines. Artificial intelligence (AI) and the Internet of Things (IoT) are set to enhance predictive maintenance and autonomous decision-making capabilities, reducing downtime and increasing uptime. Advanced robotics will continue to push the boundaries of what machinery can accomplish, while data analytics will offer deeper insights into optimizing every facet of production. As these technologies evolve, so too will the industry's ability to meet even more rigorous standards, ushering in a new era of precision and efficiency.
The path to implementing high-precision assembly lines begins with a meticulous assessment and planning phase. It necessitates identifying areas primed for improvement, establishing clear objectives, and mapping out the necessary technological upgrades. Investment in state-of-the-art machinery, sensors, and control systems forms the bedrock of this transformation. Continuous monitoring and iterative improvements ensure the system remains aligned with evolving industry standards, constantly pushing the envelope of what is possible.
In conclusion, aligning with industry standards through the use of high-precision assembly lines offers boundless long-term benefits for both manufacturers and consumers. By embracing these advanced technologies, industries can not only meet but surpass established benchmarks, delivering products of unparalleled quality and consistency. Encouraged by tangible successes across multiple domains, it becomes evident that the future of manufacturing lies in precision. Manufacturers poised to adopt these innovations stand to gain a competitive edge, fostering an environment of excellence that drives growth and elevates customer satisfaction.
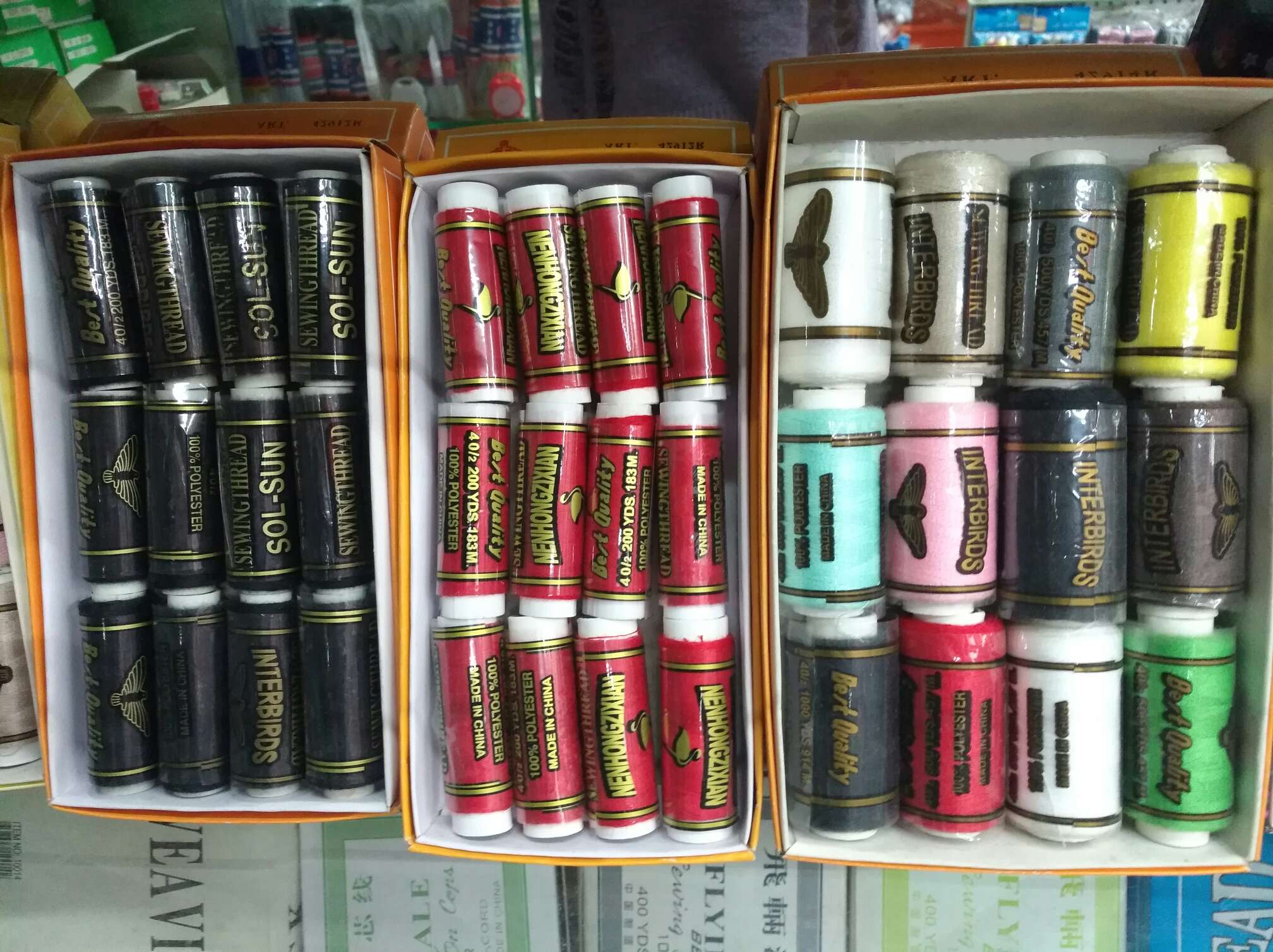