
The Birth of the Assembly Line
The early Industrial Revolution was marked by significant innovations that laid the groundwork for modern manufacturing processes. As industries transitioned from manual labor to mechanized production, initial attempts at streamlining tasks illustrated the potential of machinery in transforming industrial operations.
During this period, equipment such as spinning jennies and mechanical looms showcased how repetitive tasks could be automated to increase efficiency. Despite these advancements, it wasn't until the 20th century that the concept of the assembly line truly revolutionized production.
Henry Ford’s Vision
Henry Ford, an automotive pioneer, brought a transformative vision to life. Born on July 30, 1863, Ford displayed an early penchant for mechanics, which led him to work as an engineer before founding the Ford Motor Company. Inspired by his desire to make automobiles affordable for the masses, Ford introduced the moving assembly line to automobile production in 1913. This innovation cut production time significantly, slashing costs and making cars accessible to a broader audience.
Ford implemented several key principles in his assembly lines, including standardization of parts and worker specialization, laying the foundation for mass production as we know it today. His methods not only increased productivity but also reduced downtime and waste, setting new standards for industrial efficiency.
Transforming Manufacturing
Efficiency and Productivity Gains
The introduction of the moving assembly line drastically reduced the production time of the Model T, bringing it down from over 12 hours to just about 90 minutes per vehicle. This leap in efficiency resulted in lower production costs, directly impacting automobile affordability and enabling the car's widespread adoption.
Standardization and Specialization
By utilizing standardized parts, Ford ensured consistency and interchangeability across all units, simplifying repairs and maintenance. Additionally, dividing labor into specialized tasks allowed workers to become highly skilled in specific areas, further boosting efficiency while reducing errors and inconsistencies.
Worldwide Adoption and Adaptation
Global Influence
The success of Ford's assembly line model inspired other industries worldwide to adopt similar techniques. From consumer electronics to household appliances, the methodology spread beyond the automotive sector, becoming a cornerstone of modern manufacturing. Manufacturers around the globe adopted and adapted the assembly line technique, tailoring it to their unique production requirements.
Cultural and Economic Impact
The global proliferation of assembly lines transformed labor markets, leading to the creation of millions of jobs and altering employment landscapes. Economically, the ability to produce goods at scale fueled industrial growth and stimulated consumer culture, making products previously considered luxuries widely available.
Innovations Beyond Ford
Post-World War II Developments
Technological progress post-World War II spurred further advancements in assembly line methodologies. The integration of robotics and computer-controlled machines in the late 20th century enabled greater precision and automation, enhancing productivity and allowing even more intricate products to be manufactured efficiently.
Lean Manufacturing and Just-In-Time Production
Japanese automaker Toyota redefined manufacturing efficiency through lean manufacturing principles and just-in-time (JIT) production systems. These approaches focused on minimizing waste and ensuring timely resource availability, significantly improving operational efficiency and responsiveness to market demands.
Modern-Day Assembly Lines
Industry 4.0 and Smart Manufacturing
The current era of Industry 4.0 sees the convergence of IoT, AI, and advanced robotics within assembly lines. Real-time data analytics facilitate predictive maintenance and optimize workflows, while smart sensors enhance decision-making accuracy, resulting in more resilient and adaptive manufacturing ecosystems.
Sustainability and Environmental Considerations
Modern manufacturers are increasingly prioritizing sustainability, seeking to balance efficient production with environmental stewardship. Efforts include reducing carbon footprints, adopting renewable energy sources, and exploring circular economy models to minimize waste and pollution in production processes.
Challenges and Future Directions
Emerging Technologies
With rapid technological advancements, emerging technologies like 3D printing and additive manufacturing offer new possibilities for custom and complex part production. Augmented reality (AR) and virtual reality (VR) are reshaping training programs and design processes, providing immersive tools for workforce development.
Workforce Evolution
The evolving landscape requires shifts in workforce skills, prompting a growing focus on upskilling and reskilling initiatives. Automation and AI bring concerns about job displacement, necessitating proactive strategies to equip workers with the expertise needed for tomorrow's manufacturing environment.
Reflections on a Century of Innovation
Legacy of Henry Ford
Henry Ford's pioneering principles remain relevant, underscoring the enduring significance of efficiency, specialization, and standardization in manufacturing. Lessons learned from over a century of assembly line evolution continue to guide today's manufacturing innovations.
Looking Ahead
The future of manufacturing promises ongoing advancements in technology and process optimization. As industries strive for ever-greater efficiencies, the quest for innovative solutions remains unceasing, driven by the legacy of pioneers like Ford and the perpetual pursuit of excellence.
Learn more about our high-quality needle and thread products from the Assembly Line company.
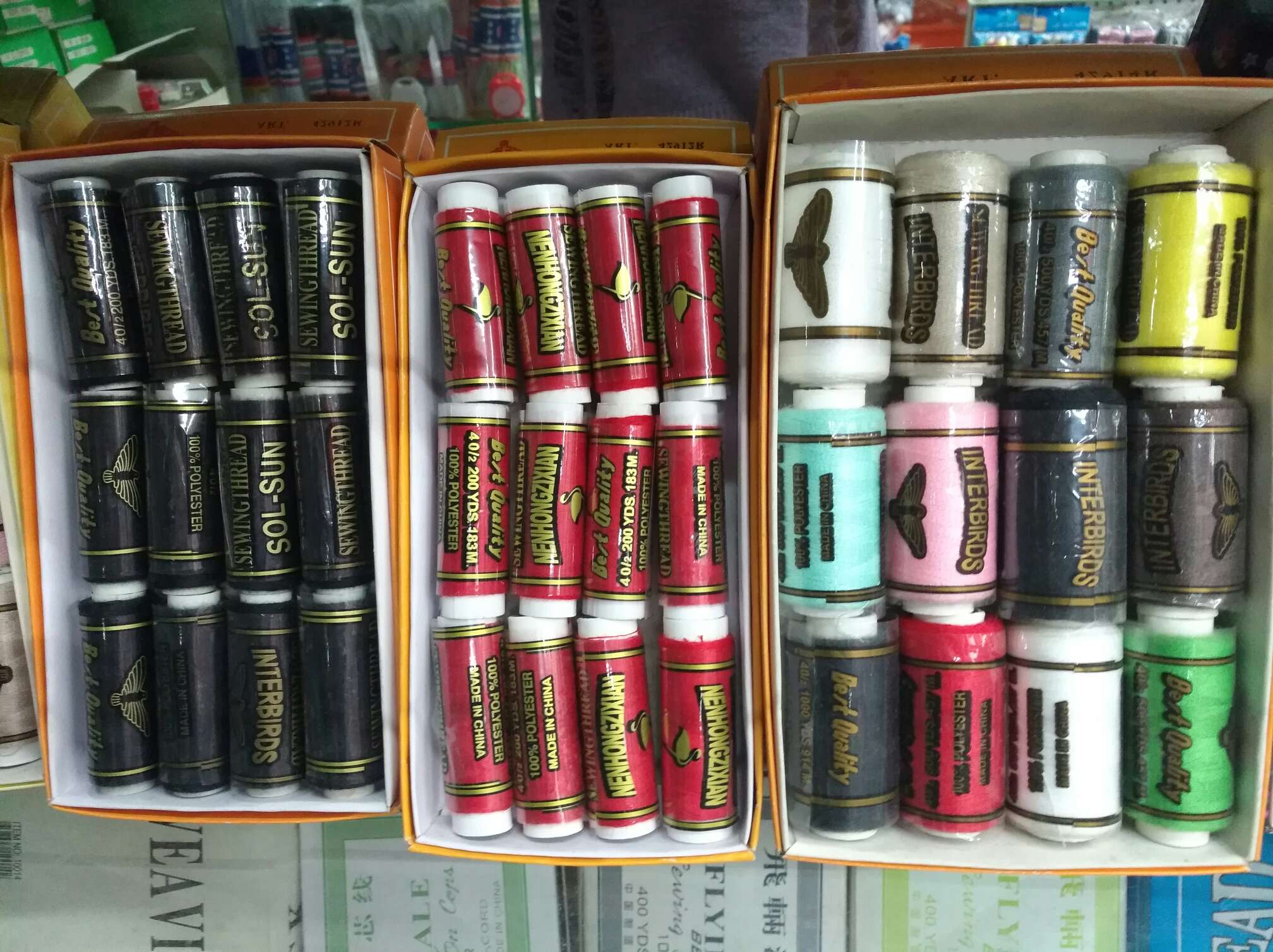